Exploring Die Casting and Injection Moulding in Modern Manufacturing
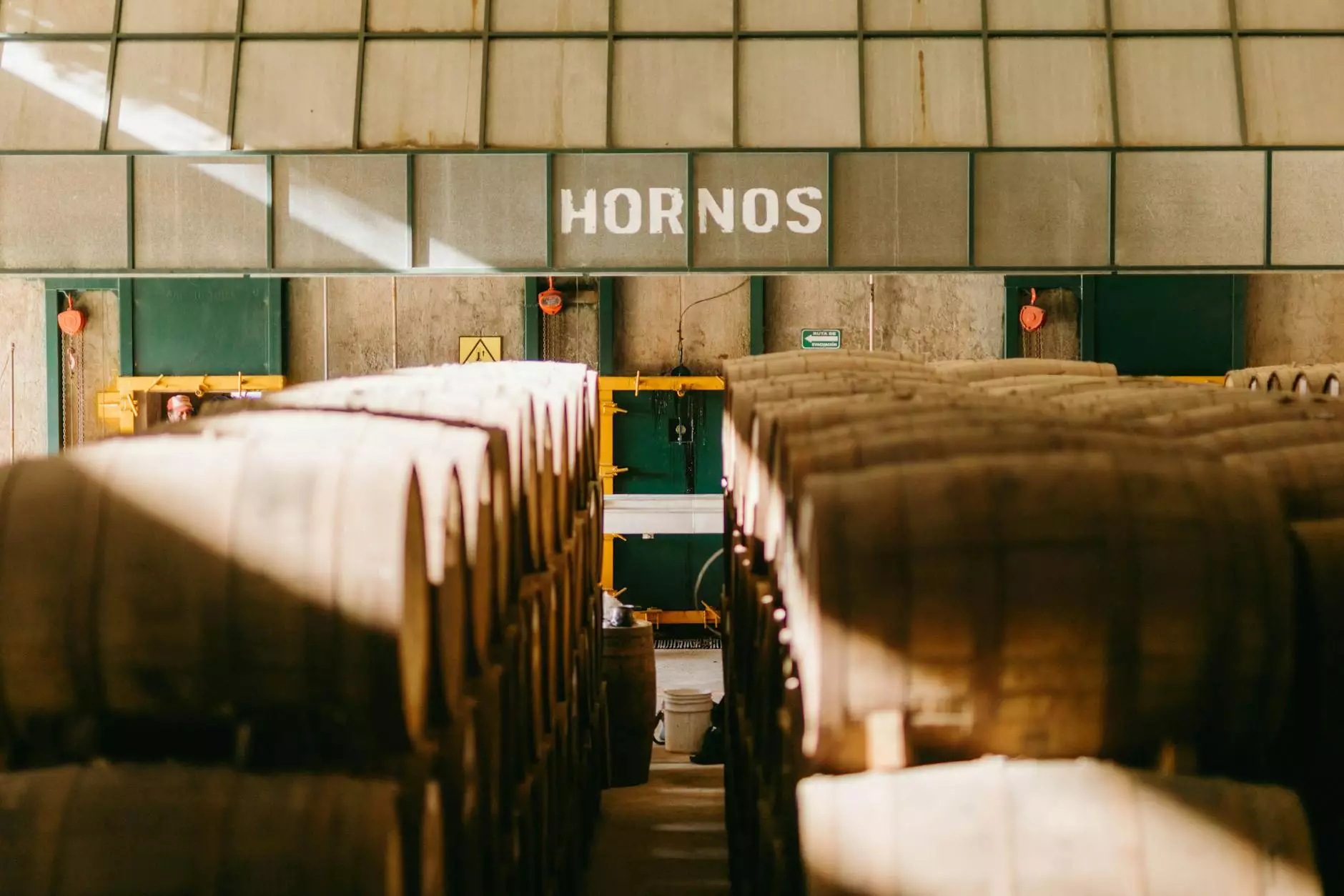
Die casting and injection moulding are two of the most pivotal manufacturing techniques used in the production of metal and plastic components. These methods have revolutionized the ways in which businesses operate, offering unparalleled efficiency, precision, and versatility. This article delves deeply into both processes, emphasizes their significance in the manufacturing sector, and illustrates how companies like DeepMould.net utilize these methods to propel themselves to the forefront of the industry.
Understanding Die Casting
Die casting is a process that involves forcing molten metal into a mold cavity under high pressure. The process is favored for its ability to produce parts with intricate details and excellent dimensional accuracy.
Types of Die Casting
There are two primary methods of die casting:
- Hot Chamber Die Casting: This technique is ideal for alloys with low melting points, such as zinc, and is characterized by quick production cycles.
- Cold Chamber Die Casting: Used for metals with higher melting points, such as aluminum, this method requires the metal to be melted in a separate furnace before being injected into the die.
The Die Casting Process
The die casting process can be broken down into several key steps:
- Preparation: The mold is coated with a release agent to facilitate removal of the part.
- Melting: Metal is melted in a furnace.
- Injection: The molten metal is injected into the mold under high pressure.
- Cooling: The metal is allowed to cool and solidify, forming the part.
- ejection: Once cooled, the part is ejected from the mold.
Advantages of Die Casting
Die casting offers numerous advantages, making it a popular choice amongst manufacturers:
- High Precision: Allows for complex geometries, ensuring each piece is manufactured to exact specifications.
- Rapid Production: Capable of producing large volumes quickly, which is crucial in meeting market demands.
- Minimized Waste: The process is highly efficient, producing less scrap material than other fabrication techniques.
The Power of Injection Moulding
Injecting moulding is similar to die casting, but it primarily works with thermoplastics and thermosetting polymers instead of metals. This process involves injecting molten plastic into a mold to create various parts.
Types of Injection Moulding
Injection moulding can be categorized into several types:
- Standard Injection Moulding: The most common form, ideal for mass production of plastic products.
- Injection Blow Moulding: Used to create hollow plastic items by blowing air into the molten material.
- Injection Stretch Moulding: Often used to manufacture containers, this method involves stretching the material during the injection process.
The Injection Moulding Process
The injection moulding process consists of the following steps:
- Material Preparation: Plastic pellets are fed into the hopper, where they are heated until molten.
- Injection: The molten plastic is injected into the mold under high pressure.
- Cooling: The plastic is allowed to cool and solidify in the mold.
- Ejection: The finished part is ejected from the mold.
Advantages of Injection Moulding
Injection moulding brings several benefits to manufacturers:
- Versatility: Able to produce a wide range of products from simple to complex parts.
- Consistency: Ensures uniformity across production runs, vital for high-quality outputs.
- Low Labor Costs: The process is largely automated, which reduces labor costs significantly.
Comparing Die Casting and Injection Moulding
While die casting and injection moulding serve similar purposes in manufacturing, they have distinct differences that can influence a company's choice of technique. Here’s a comparison of key factors:
FactorDie CastingInjection MouldingMaterials UsedMetal alloysPlasticsProduction RateHighVery HighCost EfficiencyBest for large batchesBest for medium to large batchesPart StrengthHigh strengthModerate to high strengthApplications of Die Casting and Injection Moulding
Both die casting and injection moulding find applications in various industries:
Automotive Industry
In the automotive sector, die casting is used to create engine blocks, transmission cases, and other critical components. Injection moulding supplies a range of plastic parts, including dashboards, bumpers, and interior components.
Consumer Electronics
Both processes are instrumental in producing components for consumer electronics, such as housings, connectors, and precision parts, ensuring durability and reliability in everyday devices.
Medical Devices
In the medical field, die casting provides robust components for devices, while injection moulding allows for the creation of sterile, single-use plastic parts, crucial for maintaining safety and hygiene.
The Future of Die Casting and Injection Moulding
The future of die casting and injection moulding looks promising. With advancements in technology, including the integration of automation and AI, these processes are becoming more efficient and precise. Innovations in materials and techniques are also enhancing the capabilities of both methods, allowing for lighter, stronger, and more complex parts.
Conclusion
Die casting and injection moulding are essential parts of the modern manufacturing landscape, significantly impacting productivity and quality. With businesses like DeepMould.net leading the way, the potential applications of these techniques continue to expand, paving the path for innovative solutions in various industries. Understanding the nuances of these processes not only helps businesses optimize their production but also drives forward the evolution of manufacturing as a whole.
By leveraging the unique advantages of die casting and injection moulding, companies can achieve a competitive edge in their markets, ensuring they meet consumer demands with precision and efficiency.